OUR SERVICES
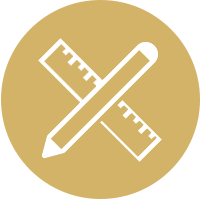
Design
Design is crucial. Design is everything. We have a team of immensely creative & innovative designers who create novel & attractive designs. Our designers take inspiration from nature, life & current international fashion trends and create exceptional designs which are love at first sight. We also develop new ideas according to our customers vision & specs. We add value to our customers design teams and enhance their product while keeping true to their brand identity.
Research & Product Development
R&D is an important part of the supply chain and we provide 100% proprietary development down to the fiber level for our largest buyers. Our mill partners and factories are working with us daily bringing new techniques and stitching to present to all our buyers. Of course, we also assist all our buyers with their own ideas developing samples and adjusting them as needed, even using the latest 3d techniques with appropriate categories.

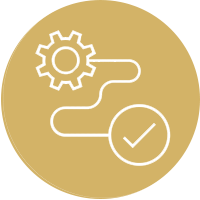
Pre-Production Department
Pre-Pro is where more than 80% of all problems are solved. As it should be, this means we solve them before production begins. We do this in several ways. We ask the right questions early in the process. This is based on our expertise of the pain points associated with the production each buyer specifically needs. We go over technical documents with a fine-toothed comb, correcting any mistakes and commenting on areas we feel could be beneficial to production, lead-time, quality or any other key element of the process. We point out milestone dates. These dates are built around progress that could impact delivery if they are not met ahead of order confirmation. We are in the factory when the production is beginning to be delivered to the teams in order to answer all the questions that inevitably arise at this moment.
Production
We go to production after all required approvals are complete. In the days leading up to this point, we take all necessary steps to get approval for all the tech packs, sewing instructions, trim details, packaging instructions, key milestone production dates and important notes related to the order. Without complete approval, production cannot begin.
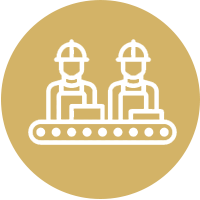

Compliance Services
Compliance standards are more important than any other part of what we do and we put tremendous effort into making sure our entire supply chain has similar values. We are not supporting factories that do not support their employees. Covid-19 has strengthened our commitment to the most vulnerable workers in our supply chain.
Quality Control
The presence of our QA Team at the factory is crucial. They inspect the production at every stage, according to A.Q.L. standards set forth prior to production.
We maintain a pro-active approach towards identification of problems, and corrective measures are taken immediately to ensure timely deliveries. Our quality monitoring system has 3 stages:
Pre-Production Check (PREPRO)
Risks are reduced by checking at this very first stage.
During Production Check (DUPRO)
Inspection during production is carried out to check and verify that the initial discrepancies have been rectified and to ensure the average quality standard of production runs. These are carried out weekly or bi-weekly depending on the product.
Final Random Inspection (FRI)
Final random inspection is carried out when the total consignment is packed and ready for shipment. FRI is performed according to the AQL standards preferred by our client partner for both measurements and quality. The detailed physical inspection of the samples selected at random is based on detailed specifications of our client partner to confirm all standards.

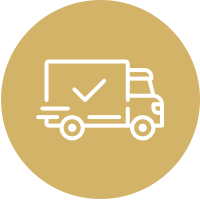
Shipment & Delivery
Once production is complete and has passed the FRI, we focus on logistics. We offer full logistic support to our buyers, coordinating with relevant shipping service providers, making sure the goods arrive on time all the way to our client’s “doorstep”.